离子电池的容量从早期的600mAh、1000mAh到现在,高达6000mAh、10000mAh,为了实现更快的充电速度,降低充电时间,通常采用提高电流、使用大电流充电的快充技术,那么,大电流充电,对电池包内的功率MOSFET就提出了更高的技术要求;另外,大容量锂离子电池在生产线和使用过程中,还有一些特定的技术要求,所有这些因素,都对大容量锂离子电池包内的充、放电管理的功率MOSFET提出了严格的技术设计挑战。
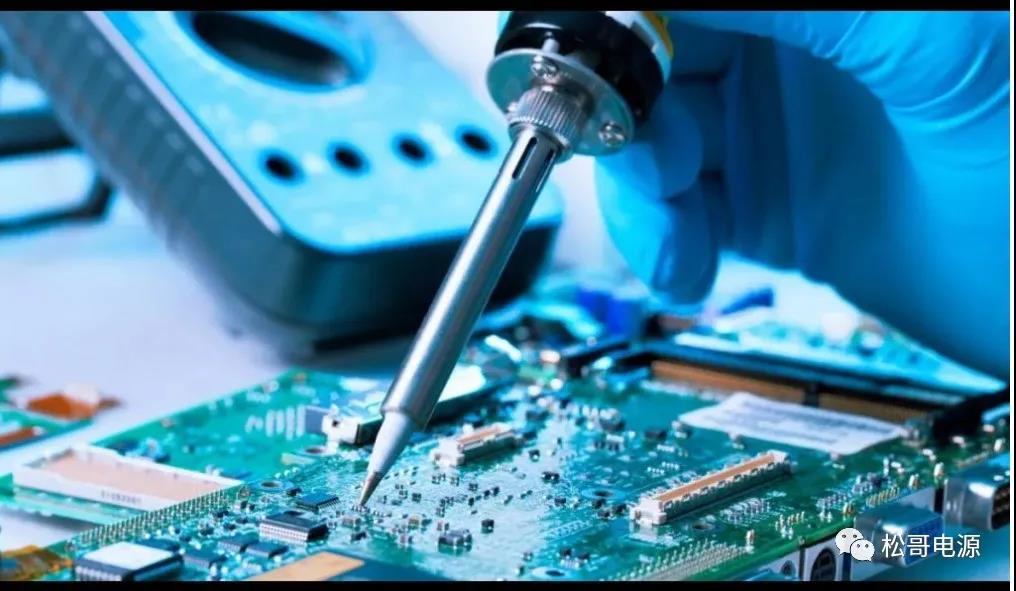
4.1、高功率密度、低功耗、散热好
大容量锂离子电池包设计基本的要求就是在一定的体积和重量的条件下,尽可能提高电池的容量,从而提高功率密度,由于其空间非常有限,因此,要求其充、放电管理PCM控制板以及其上面的功率MOSFET,都应该具有更小的体积和尺寸;同时,由于快充时的电流大,要求功率MOSFET在一定的尺寸的限制下,如1.2mm*1.2mm,具有最小的导通电阻RDS(ON)。理论上,更小的RDS(ON)要求更大的晶片尺寸。对于同样的晶片尺寸,实现更低的RDS(ON),设计上主要从二个方面进行优化。
4.1.1、晶圆技术
为了使功率MOSFET实现更低的导通电阻RDS(ON),就必须对功率MOSFET内部的结构重新设计,使用各种最新技术,降低内部单元结构的晶胞尺寸,提高晶胞单元的密度;同时,改变内部的电场分布,在保证同样的耐压的前提,尽可能降低晶片的厚度,这样,功率MOSFET实现超低的FOM值,获得更低的导通电阻RDS(ON)。
4.1.2、封装技术
通常功率MOSFET封装使用引线,为了进一步降低导通电阻,在PCM中,使用新的芯片级CSP的封装技术,从而完全去除封装连线电阻。同时,芯片级CSP的封装技术,具有更低的热阻,热量更容易传导出去,降低功率MOSFET的温度,提高了其可靠性。
采用CSP封装技术的功率MOSFET,由于没有外部塑料壳等材料的保护,在PCM生产加工的过程中,如PCB板焊接过程中,会受到各种热应力、机械应力的作用,产生开裂的风险大,因此,要采用各种新技术,如在功率MOSFET晶片的表面涂敷新材料,保证其抗机械应力和热应力的能力,提高可靠性。
4.2、抗短路的能力
大容量锂离子在应用中,在极端条件下,如遇到输出负载短路,那么,电池包的输出端短路后,电池就会流过非常大的电流,IC检测到输出过流后,要延时一段时间才能做出保护动作,那么在延时的时间内,由于MOSFET的工作电流非常大,这就要求MOSFET具有承受大电流冲击的能力。因此,现在安规的要求,所有的锂离子电池都会做短路测试,以免电池发生爆炸。
(a)短路测试通过 (b)短路测试失败
理论上,晶片尺寸越大,抗短路冲击的能力越强。在非常小的晶片尺寸的限制条件下,需要对功率MOSFET的内部结构做特定的设计,保证其具有足够的抗短路大电流冲击的能力。
4.3、抗雪崩能力
功率MOSFET的雪崩能力表明器件的强状程度和可靠工作能力,特别是电池包的输出端短路关断后,非常容易发生雪崩。这也要求需要对功率MOSFET的结构做优化,保证其具有足够的雪崩能力。
(a)雪崩测试通过 (b)雪崩测试失败
图20:雪崩测试波形
4.4、高的抗dV/dt能力
大容量锂离子在生产过程中,外部的测试直流电源会直接碰触电池包的二个输出端,电路不发生损坏的直接碰触的电压越高,能力越强。这个测试,实际测量的是MOSFET对于dV/dt的耐受能力;而且,在电池包输出短路、保护关断过程中,也会有一个非常大的动态的dV/dt,过大的dV/dt会引起功率MOSFET的动态雪崩损坏。因此,需要对功率MOSFET的结构做优化,保证其具有高的直接碰触电压和抗dV/dt的能力。
(a)13V测试通过 (b)14V测试失败
4.5、高的抗ESD能力
PCM在生产和使用的过程中,器件需要有足够强的EDS的能力,在非常小的晶元尺寸的限制条件下,保证其具有足够强的EDS的能力,同时具有其他的性能,如低的RDS(ON),都需要对功率MOSFET的结构进行优化。
5、PCM的PCB及热设计要点
由于PCM控制板一般都是和电池组装在一起,要求PCB尺寸比较小,发热量也不能过高,一般手机应用要求MOSFET在常温环境、满载条件下表面温度不超过65度。BMS系统可以容忍更高的温升。
下面以手机快充47W方案为例,充电电压5V,最大充电电流9.4A。需要并联两颗AOCR38232 (0.8毫欧),电流路径采用上下对称,保持电流均衡。两颗MOSFET之间间隔3厘米,避免相互加热。尽可能的增加功率路径铺铜面积,并且在靠近MOSFET的铜皮上增加散热孔以增加散热,减小MOSFET温升。
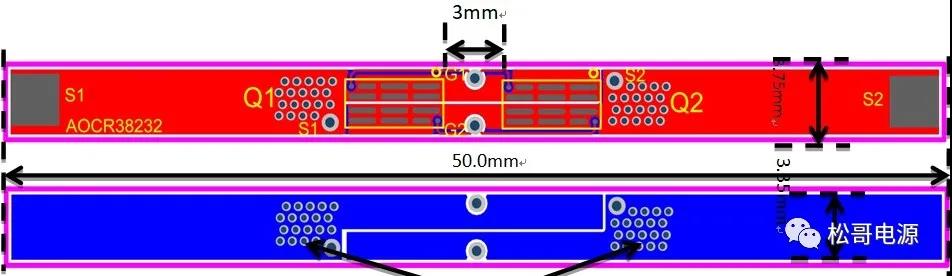
图22:PCM电路板
用红外测温仪测量MOSFET表面温升,由于不同的器件的表面材质不同,产生的光学折射率也不同。AOS普遍使用硅作为表面材质,而有些竞争对手使用金属材料。金属的光学折射率低于硅,所以使用红外测量温度时,金属表面材质的器件会表现出更低的温升,但真实的温升并不是如此。
这就要求用红外测试仪测量MOSFET表面温升时,需要先用光学折射率接近100%的黑色油漆喷涂器件表面,然后再进行测试,这样才能得到更准确的温升数据,避免由于材质的不同而导致测试误差。
图23的结果显示,喷涂黑漆后,AOS产品测得的温升增加了1.3度,而金属表面材质的器件,测得的温度增加了11.3度。
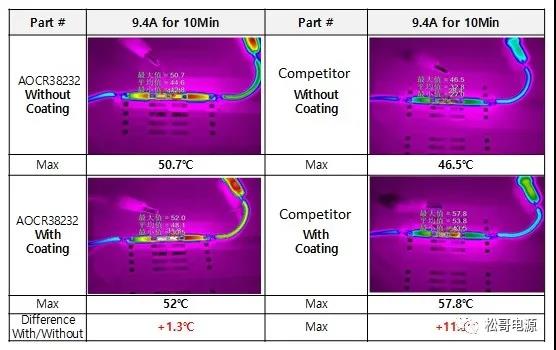
图23:PCM板的MOSFET温度测量
6、输出漏电流产生原因及解决方法
6.1、输出漏电流产生的原因
漏电流问题产生的原因:在电池包生产过程中。当电池端B+、B-有电压时,充电管和放电管处于关闭状态。这时候如果放电管有微小的漏电流,比如100nA,由于输出端并没有负载,输出端呈现高阻抗状态,比如10兆欧,此时芯片会检测输出端有1V的电压。以BQ20Z45为例,当输出P+、P-之间电压高于0.8V时,芯片会误判定输出有充电电压,会启动预充电功能,开启充放电管,尝试给电池充电。从而导致芯片开始工作,电池的静态损耗增加,严重时会导致电池电量耗尽。
以常见的30V充放电管为例,通常数据表会表示30V的IDSS小于1uA, 实际的笔记本电脑电池应用中,电池电压通常在9V-13.2V之间。如上述案例中,很难判断器件在13.2V的电池电压下,放电管的DS漏电流是不是大于100nA,这样就很有可能导致充放电管漏电流过大,从而耗光电池电量的情况。
同时,MOSFET厂家在出厂测试IDSS的时候,使用的是300uS的脉冲电压,是短时间的漏电流测试。工厂的短时间脉冲测试无法保证长时间偏压情况下的漏电流,从而导致极少量的MOSFET在使用过后IDSS超出数据表的现象发生,也导致器件漏电流过大。
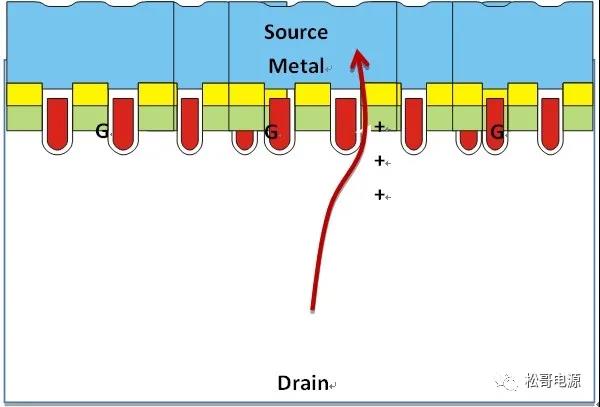
图24:器件漏电电流示意图
6.2、输出漏电流的解决办法
由于实际系统中,电池板的输出端连接到主板,主板上的电容,电阻,芯片等器件都有一定的漏电流。主板的电池输入接口测量阻抗普遍低于1兆欧,上述漏电流异常问题,在系统上并不会发生不良,只是在电池包厂家库存期间可能发生电池电量异常下降的问题。
漏电流问题的解决办法:
方案一:建议电池包输出端P+、P-并联1兆欧姆电阻,模拟实际客户实际应用情况,可以有效的避免因为芯片误检测而导致的问题。
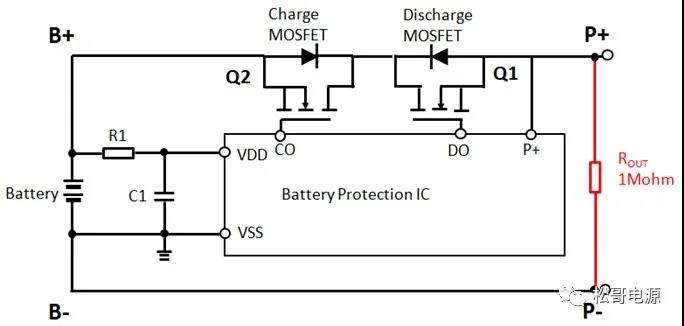
图25:漏电流的解决方案
增加1M欧姆电阻后,P+端的漏电流产生的漏电压下降到0.46V,如表1所示,内部MOSFET不会被开通,系统正常。
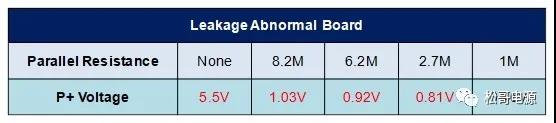
表1:增加外部电阻后的电压
增加电阻的不利之处就是会导致电池弱放电,放电的电流为:0.46V/1M=0.46uA。这个电阻放电消耗的电量非常小,使用4100mAH的电池笔记本电脑,10年的消耗的电量不到电池容量的1%,可以忽略。1M欧姆的放电电阻,也可以放在电池生产线的测试工位。
方案二:建议芯片调整输出检测电压,单节电池建议从0.8V提高到2.3V,3节串联电池建议提高到6V,这样可以容忍更高的放电管的漏电流,系统也不会开通内部的MOSFET。
评论